Steel Characteristics
There are ten principal characteristics that customers consider when buying steel. These characteristics are controlled by the addition / elimination of various elements in the steel making process. The effects of various elements on steel are discussed here by considering the elements individually. In practice, however, the effect of any particular element will often depend on the quantities of other elements also present in the steel. For example, the total effect of a combination of alloying elements on the hardenability of steel is usually greater than the sum of their individual contributions. The ten characteristics are: strength, hardness, hardenability, machinability, toughness, ductility, weldability, fatigue resistance, wear resistance and corrosion resistance.
Carbon is the principal hardening element in steel, with each additional increment of carbon increasing the hardness and tensile strength of steel in the as-rolled or normalized condition. For improved ductility, weldability and toughness levels: a carbon content below 0.20% is preferred. A compromise must be maintained between the higher carbon level required for tensile properties, and lower carbon levels associated with improved ductility, weldability and toughness.
Characteristics: strength, hardness, hardenability and wear resistance.
Silicon is one of the principal deoxidisers used in the manufacture of both carbon and alloy steels, and depending on the type of steel, can be present in varying amounts up to 0.40% as a result of deoxidation. Silicon is also a ferrite strengthener.
Characteristics: strength.
Chromium is used in constructional alloy steels primarily to increase hardenability, provide improved abrasion-resistance and to promote carburization. Of the common alloying elements chromium is surpassed only by carbon, manganese and molybdenum in its effect on hardenability. Chromium forms the most stable carbide of any of the more common alloying elements, giving high-carbon chromium steels exceptional wear-resistance. Because its carbide is relatively stable at elevated temperatures, chromium is frequently added to steel used for high temperature applications.
Characteristics: hardenability, wear resistance and corrosion resistance.
Sulphur is generally considered an undesirable element except where machinability is an important consideration and resulphurised steels may be ordered. Whereas sulfides in steel act as effective chip-breakers to improve machinability, they also serve to decrease transverse ductility and impact strength. Moreover, increasing sulphur impairs weldability and has an adverse effect on surface quality.
Characteristics: machinability.
Vanadium increases strength, hardness, and resistance to shock impact. It retards grain growth, permitting higher quenching temperatures. It also enhances the red hardness
Manganese is present in all commercial steels, and contributes significantly to steel’s strength and hardness in much the same manner, but to a lesser extent, than does carbon. Its effectiveness depends largely upon, and is directly proportional to, the carbon content of the steel. Another important characteristic of this element is its ability to decrease the critical cooling rate during hardening, thereby increasing the steel's hardenability. Its effect in this respect is greater than that of any of the commonly used alloying elements.
Characteristics: strength, hardenability and wear resistance.
Nickel is one of the fundamental steel-alloying elements. When present in appreciable amounts, it provides improved toughness, particularly at low temperatures. Nickel lowers the critical temperatures of steel, widens the temperature range for effective quenching and tempering, and retards the decomposition of austenite. In addition, nickel does not form carbides or other compounds, which might be difficult to dissolve during heating for thermal treatment. Because of the tight adherent scale formed on reheating nickel-containing steels, the surface quality of bars with nickel is somewhat poorer than bars without nickel.
Characteristics: strength, toughness and fatigue resistance.
Molybdenum exhibits a greater effect on hardenability per unit added than any other commonly specified alloying elements except manganese or boron. It is a non-oxidising element, making it highly useful in the melting of steels where close hardenability control is desired. Molybdenum is unique in the degree to which it increases the high-temperature tensile and creep strengths of steel. It is also used to reduce steel's susceptibility to temper brittleness.
Characteristics: strength, toughness and hardenability.
Phosphorus is generally considered an impurity except where its beneficial effect on machinability and resistance to atmospheric corrosion is desired. While phosphorus increases strength and hardness to about the same degree as carbon, it also tends to decrease ductility and toughness, or impact strength, particularly for steel in the quenched and tempered condition. The phosphorus content of most steel is therefore kept below specified maxima, which range up to 0.04%.
Characteristics: strength, hardness, machinability and corrosion resistance.
Tungsten increases strength, hardness, and toughness; tungsten steels have superior hot-working and greater cutting efficiency at elevated temperatures.
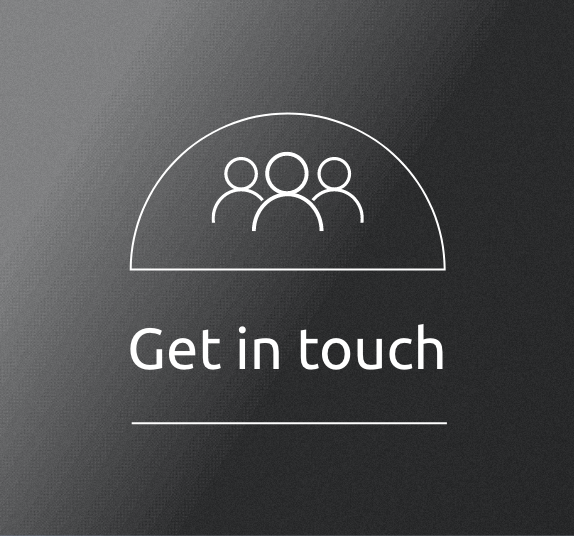
Supporting our clients